The narrow-face of the mold should be tapered to match the shrinkage of steel shell, which is cooling against the wide face.Shrinkage depends mainly
on the surface temperature of the shell and the steel grade. The model predicts ideal average taper, by dividing the thermal strain, ε, by distance down the mold (instantaneous taper) or by the mold length (total taper per m). Thermal shrinkage strain is estimated here εth1, by:
ε th1 = TLE(Tsol ) −TLE(Ts )
Here, TLE is the thermal linear expansion function for the given steel grade,Tsol : solidus temp.(1509), Ts : shell surface temp.
TLE(Tsol) =α (T −Tsol ) , α is thermal linear expansion co-efficient
calculated from
weighted averages of the phases present.
For the sample cases, the higher speed causes a hotter shell with less shrinkage, , so needs slightly less narrow face mold taper. The shrinkage εth1, based on surface
temperature only and is almost independent of casting speed, due to the cancellation effect. With a linear taper, the narrow-face shell attempts to shrink away from the upper portion of the mold, while it pushes against the lower
portion of the mold. To match the shrinkage, it is clear that taper should be increased high in the
mold and decreased lower down. Mold distortion, viscoplastic creep of the steel, and other factors should also be taken into account when designing a non-linear mold taper. These calculations require sophisticated thermal-stress models, to calculate temperatures, stresses, and shrinkage, including the formation of an air gap near the corners, and its effect on heat flow across the mold/shell interface. The calibrated CON1D model is currently being used to provide calibrated heat transfer data to these models to evaluate and improve taper optimization.

on the surface temperature of the shell and the steel grade. The model predicts ideal average taper, by dividing the thermal strain, ε, by distance down the mold (instantaneous taper) or by the mold length (total taper per m). Thermal shrinkage strain is estimated here εth1, by:
ε th1 = TLE(Tsol ) −TLE(Ts )
Here, TLE is the thermal linear expansion function for the given steel grade,Tsol : solidus temp.(1509), Ts : shell surface temp.
TLE(Tsol) =α (T −Tsol ) , α is thermal linear expansion co-efficient
calculated from
weighted averages of the phases present.
For the sample cases, the higher speed causes a hotter shell with less shrinkage, , so needs slightly less narrow face mold taper. The shrinkage εth1, based on surface
temperature only and is almost independent of casting speed, due to the cancellation effect. With a linear taper, the narrow-face shell attempts to shrink away from the upper portion of the mold, while it pushes against the lower
portion of the mold. To match the shrinkage, it is clear that taper should be increased high in the
mold and decreased lower down. Mold distortion, viscoplastic creep of the steel, and other factors should also be taken into account when designing a non-linear mold taper. These calculations require sophisticated thermal-stress models, to calculate temperatures, stresses, and shrinkage, including the formation of an air gap near the corners, and its effect on heat flow across the mold/shell interface. The calibrated CON1D model is currently being used to provide calibrated heat transfer data to these models to evaluate and improve taper optimization.
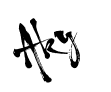
No comments:
Post a Comment