Below the mold, heat flux from the strand surface varies greatly between each pair of support
rolls according to spray nozzle cooling (based on water flux), hspray; radiation, hrad_spray; natural
convection, hconv; and heat conduction to the rolls, hroll, as shown in Fig. Incorporating these
phenomena enables the model to simulate heat transfer during the entire continuous casting
process. The heat extraction due to water sprays is a function of water flow, of the following
form:
spray water h(spray) = A⋅Qwater ⋅(1 − b⋅Tspray)
where Qwater (l/m2s) is water flux in spray zones, Tspray is the temperature of the spray cooling
water. In Nozaki’s empirical correlation, A=0.3925, c=0.55, b=0.0075, which has been used
successfully by other modelers.
Radiation is calculated by:
hspray =σ ⋅ε steel(Tsk +Tambk) (Tsk +T2 spray)
where TsK and TsprayK are Ts and Tspray expressed in Kelvin. Natural convection is treated as a
constant input for every spray zone. For water-cooling only, it is not very important, so was
simplified to 8.7W/m2K everywhere. Larger values can be input for hconv to reflect the stronger
convection when there is air mist in the cooling zone. Heat extraction into the rolls is calculated
based on the fraction of heat extraction to the rolls, froll, which is calibrated for each spray zone:
hroll = [(hrad_spray+hconv + hspray)*Lspray +(hrad_spray + hconv)*(Lsparay_pitch-Lspray-Lrollcontact)/Lroll contact*(1-froll)]*froll
A typical froll value of 0.05 produces local temperature drops beneath the rolls of about 100oC.
Beyond the spray zones, heat transfer simplifies to radiation and natural convection.

rolls according to spray nozzle cooling (based on water flux), hspray; radiation, hrad_spray; natural
convection, hconv; and heat conduction to the rolls, hroll, as shown in Fig. Incorporating these
phenomena enables the model to simulate heat transfer during the entire continuous casting
process. The heat extraction due to water sprays is a function of water flow, of the following
form:
spray water h(spray) = A⋅Qwater ⋅(1 − b⋅Tspray)
where Qwater (l/m2s) is water flux in spray zones, Tspray is the temperature of the spray cooling
water. In Nozaki’s empirical correlation, A=0.3925, c=0.55, b=0.0075, which has been used
successfully by other modelers.
Radiation is calculated by:
hspray =σ ⋅ε steel(Tsk +Tambk) (Tsk +T2 spray)
where TsK and TsprayK are Ts and Tspray expressed in Kelvin. Natural convection is treated as a
constant input for every spray zone. For water-cooling only, it is not very important, so was
simplified to 8.7W/m2K everywhere. Larger values can be input for hconv to reflect the stronger
convection when there is air mist in the cooling zone. Heat extraction into the rolls is calculated
based on the fraction of heat extraction to the rolls, froll, which is calibrated for each spray zone:
hroll = [(hrad_spray+hconv + hspray)*Lspray +(hrad_spray + hconv)*(Lsparay_pitch-Lspray-Lrollcontact)/Lroll contact*(1-froll)]*froll
A typical froll value of 0.05 produces local temperature drops beneath the rolls of about 100oC.
Beyond the spray zones, heat transfer simplifies to radiation and natural convection.
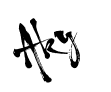